It's generally not a great idea to remove rings from a cylinder after break in and then replace without honing and new rings. You can lose the existing ring seal.
I have done this and had it go OK and I've also had it not work out.
A good friend of mine who is a master machinist and motorcycle builder goes to great lengths to keep the rings in the bore when doing a bottom end inspection. He has made a jig so that he can lift the Vincent cylinders just enough to pull the gudgeon pins and check rod wobble ( Big end bearing wear state) while keeping the pistons and rings in the cylinders, engine still in bike.
This text from a small aircraft engine maintenance article gives an explanation.
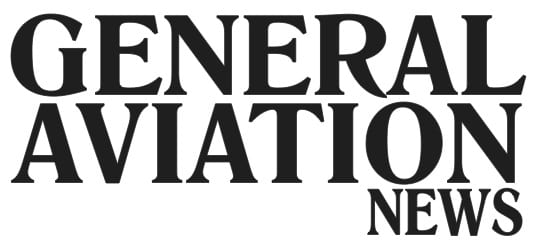
GENERAL AVIATION NEWS
Because flying is cool
MENU
The marriage between piston rings and cylinder wall
By
Paul McBride · June 3, 2012 ·
Q: I am an A&P, and have been in aviation since 1990. I once worked with another mechanic who told me that if you pull a piston out of a cylinder, you must replace the rings and hone the cylinder. He is the only tech I have heard say this — until I read your article
What’s best? A flush or overhaul?
You stated: “If oil starvation is suspected, you may want to remove the #1 cylinder (leave the piston in the cylinder so you don’t have to hone the cylinder and install new rings) and remove the connecting rod from the crankshaft.” Can you explain this? Is there a Service Bulletin or other directive that explains this practice? Thanks for sharing your knowledge with us.
TOM THROSSEL, via email
A: Tom, let me start off by thanking you for your question. For the life of me, I can’t recall any Lycoming publication that specifically tells you to do what I stated about leaving the piston in the cylinder while doing an internal inspection in this particular situation. In this case it was for the suspicion of foreign material in the engine. However, as I think back in my career, I honestly believe this is one of those maintenance procedures that one learns from experience.
Let’s take a look at the logical side of the equation. I hope you noticed that the person making the inquiry did not mention how many hours were on the engine in which he found bits and pieces of paper towel. Therefore, I assumed the engine was beyond the normal break-in period of, say, 25 to 50 hours. Given that, I also assumed that if this was the case, then the piston rings would have been seated or bedded in and the oil consumption stabilized. If the piston were removed from the cylinder at this time, the result would be that we disturbed the marriage between the piston rings and the cylinder wall, which is a result of proper engine break-in and which we know has occurred when the engine oil consumption stabilizes. Once the piston is removed from the cylinder barrel, you can never reassemble it and have the same ring to barrel marriage.