NickZ
VIP MEMBER
- Joined
- Oct 31, 2018
- Messages
- 457

To close the loop on my question, here is the follow up.
My issue was that I had removed the oil pump from my 1971 Roadster to see if I could reduce wet sumping. I have 3 other spare pumps, another from a 71 engine and 2 from 73 engines. I wanted to find a way to verify functionality and to compare the performance of these pumps. Then I would decide which one to put in the engine I'm working on, either with or without refurbishing.
I built 2 test rigs, neither of which is scientific in nature. These tests are not designed to measure any real world performance parameters, only go/no go function and a relative performance comparison between pumps.
The first I'll call the static test rig and my intention was to see which pump would be most resistant to allowing oil from the tank to flow to the sump. It consists of a funnel reservoir which gravity feeds a pump thru a spare timing side crankcase which has the pump under test mounted on it. My intent was to measure the amount of time it took for the 24 oz of oil in the reservoir to be emptied. I had pans to collect any oil that dripped out of the pump's feed output and out of the channel to the sump on the return side. The length of time it took to empty the reservoir lasted so long that it would empty in the middle of the night, so instead I switched to measuring the drip period, which was quite regular.
Results:
-My original pump had the longest initial drip period of around 12 seconds. The others were clustered around 7 seconds.
-No oil made it thru to the return path collection point. All the flow was a result of oil passing thru the output of the feed side of the pump, which when assembled, I presume would make it to the sump thru the crankshaft etc.
Here is a photo of the static test set up:
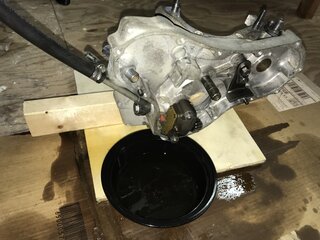
My issue was that I had removed the oil pump from my 1971 Roadster to see if I could reduce wet sumping. I have 3 other spare pumps, another from a 71 engine and 2 from 73 engines. I wanted to find a way to verify functionality and to compare the performance of these pumps. Then I would decide which one to put in the engine I'm working on, either with or without refurbishing.
I built 2 test rigs, neither of which is scientific in nature. These tests are not designed to measure any real world performance parameters, only go/no go function and a relative performance comparison between pumps.
The first I'll call the static test rig and my intention was to see which pump would be most resistant to allowing oil from the tank to flow to the sump. It consists of a funnel reservoir which gravity feeds a pump thru a spare timing side crankcase which has the pump under test mounted on it. My intent was to measure the amount of time it took for the 24 oz of oil in the reservoir to be emptied. I had pans to collect any oil that dripped out of the pump's feed output and out of the channel to the sump on the return side. The length of time it took to empty the reservoir lasted so long that it would empty in the middle of the night, so instead I switched to measuring the drip period, which was quite regular.
Results:
-My original pump had the longest initial drip period of around 12 seconds. The others were clustered around 7 seconds.
-No oil made it thru to the return path collection point. All the flow was a result of oil passing thru the output of the feed side of the pump, which when assembled, I presume would make it to the sump thru the crankshaft etc.
Here is a photo of the static test set up:
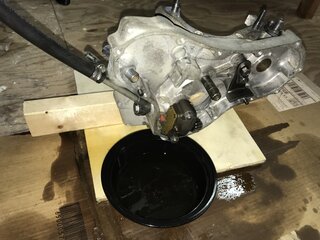